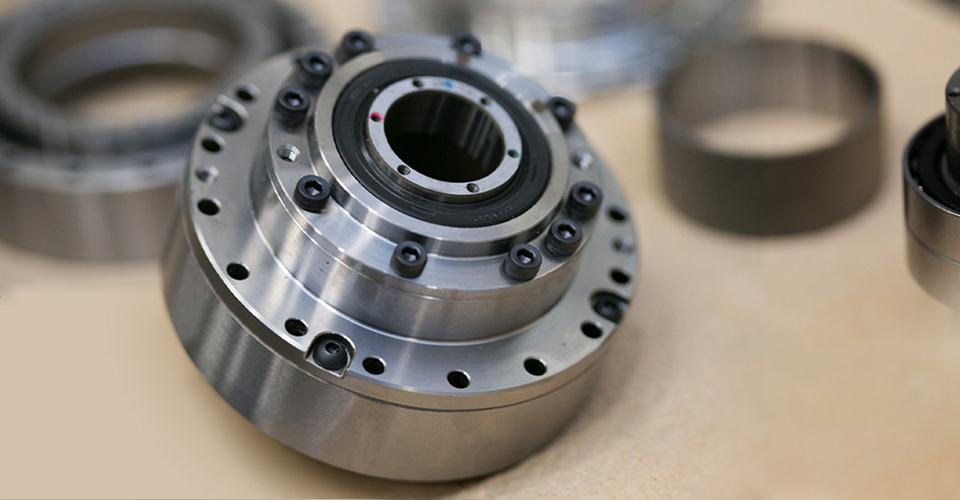
The ECY Series:A smaller Gear reducer after over 10 years of development
Due to a labor shortage in recent years, robots have increasingly been used in a variety of industrial fields. To better cope with these conditions,
there is a need for smaller robots, which in turn has meant that the Gear reducers used for the joints need to be smaller.
This is the story of how E CYCLO® High Precision Gearboxes ECY Series (hereafter, ECY Series), was developed over a period of 10 years.
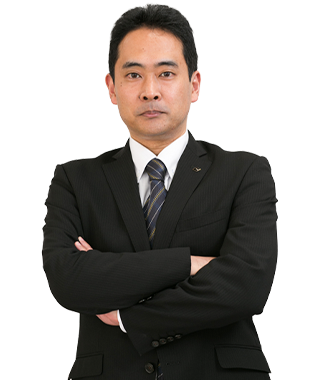
PTC Group Gearmotor
Business Division Sales
& Marketing Headquartes
Product Development Department
Product Development Section
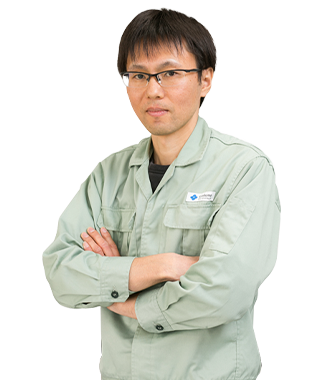
Mechanical Component Dept.
Technology Reseach Center,
Corporate Technology
Management Group
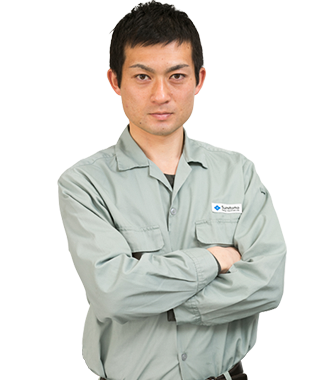
Mechanical Component Dept.
Technology Reseach Center,
Corporate Technology
Management Group
We started with accurate advice from an expert
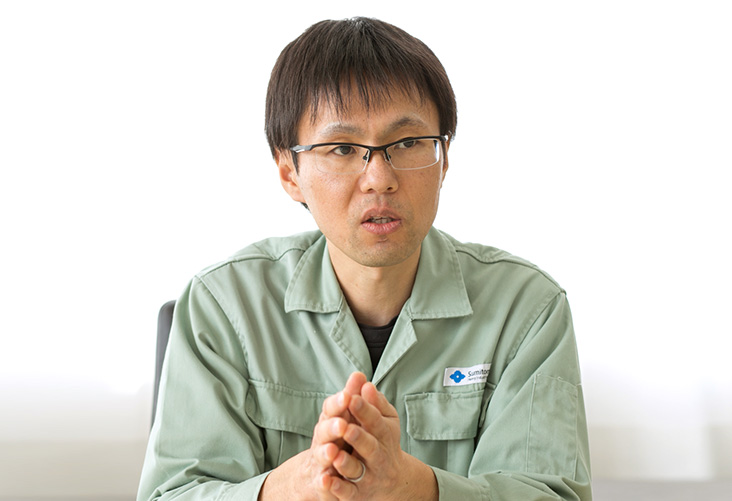
A Gear reducer reduces the speed of a motor to an appropriate level and increases its torque. While we usually cannot see Gear reducers themselves, they make our daily lives more convenient and enjoyable through their use in equipment such as ski lifts, Ferris wheels in amusement parks, elevators, train platform doors and industrial robots.
Sumitomo Heavy Industries is proud to hold the top share for power transmission and motors in Japan's industrial market. Our Gear reducers are developed to meet the needs of our customers, with a range of sizes and precision control.
Currently, the demand for robots such as labor-saving robots, Collaborative Robot and power assist suits is increasing as a solution to various problems in society. This trend calls for smaller robots to reduce costs, save space and conserve energy, and as such, Gear reducers used in these types of robots must also be made smaller.
Sumitomo Heavy Industries had not produced small precision Gear reducers at that time, so our Technology Research Center (hereafter TRC) began working on reducing the size in the late 2000s.
To provide guidance for the development process at TRC, we invited a Gear reducer expert who used to be a plant manager in the PTC Group. He served as an adviser at the time and changed to a consultant position after retirement.
Our expert had developed many kinds of Gear reducers for a long time and had a wealth of ideas and experience in this area. He was tasked with using his knowledge to develop a new type of Gear reducer and training our R&D professionals in the development of Gear reducers.
Shinji Yoshida was selected as the key person to conduct basic and elemental development for smaller Gear reducers at the TRC. Manabu Ando joined the team in the following year, and then Fumito Tanaka in the year after. Our development work was carried out by this three-person team.
Throughout the development process, they have worked toward the ambitious goal of "double and half innovation": double the performance at half the size.
The first step was to reduce the size of the CYCLO® Drive, the main product of Sumitomo Heavy Industries. This gear has been on the market for 80 years, and those decades of knowledge and technology have produced a sharply refined range for purposes from servo motors to precision control.
The CYCLO® Drive has a unique shape with smooth curvature (epitrochoid parallel curve) and pins at its meshing parts. It is characterized by its excellent lubrication properties and excellent durability. This gear would have been ideal for our size reduction project as it had been used for a wide range of applications and had a good reputation among our customers, but important factors were discovered during the development process that meant that this gear could not be reduced to the final goal size.
On discussing how Sumitomo Heavy Industries could make up for its slow start in the market by supplying a higher caliber of small and precise Gear reducers than competitors in the market, the team decided to develop a new mechanism different from that of the CYCLO® Drive.
Improving accuracy and strength
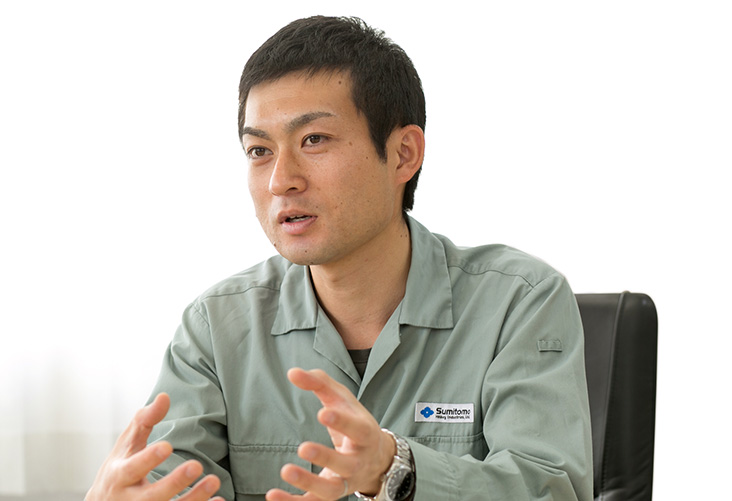
The team's idea to achieve a smaller size was a curved spline (wave gear). This has a mechanism in which a motor rotates a thin cylindrical gear that is transformed into an elliptical shape, meaning that strength is the most important element. The gears also wear more easily as they are engaged directly rather than using CYCLO® Drive type pins, making lubrication more difficult. Looking back, Shinji Yoshida (Senior Engineer, Mechanical Component Dept. Technology Research Center, Corporate Technology Management Group) says "As this was a trial using an unknown mechanism, we had no knowledge about thin gears and had significant difficulty even making the prototypes. The consultant who advised us said that it was a learning experience even for him-the project was so difficult that it was unknown territory even for an expert. Improvement of strength and lubrication were raised as key issues for the development project.
The development process was very difficult. Prototypes broke in a short time, probably because they were designed using strength calculations by a tool that was developed for the CYCLO® Drive model. For a long time, it was a cycle of reporting the test results to the consultant, discussing the matter and carrying out another trial.
Making highly accurate parts was essential for achieving sufficient strength for the new Gear reducer, because the strength would only be sufficient if the accuracy of both the gears as a whole and each part was sufficient.
Fumito Tanaka (Engineer, Mechanical Component Dept. Technology Research Center, Corporate Technology Management Group) said "In the beginning, we made trial products only to verify our theory, which came with problems such as manufacturing error in the parts. We didn't have enough knowledge and experience, so we had to use trial and error in order to consistently achieve the accuracy we needed."
The initial development phase consisted of designing the curved spline, conducting trials and evaluating the gear parts, which are the key points of reducing the size. The gears were the same trochoid tooth type used for CYCLO® Drive, with original design used to achieve the strength that was needed. The wire cut method was adopted for prototype production as it was impossible to use the conventional method, but this adapted method came with the major drawback of a level difference between the first cut gear and the last one. The team, of course, designed the gears so that there was no level difference, but the difference kept occurring nonetheless, preventing the stable and highly accurate curved spline that the team sought. As a result of the failure to consistently create gears with the same accuracy, the team was unable to evaluate the strength of the curved spline. Fewer trials were conducted due to the high processing cost, and the difference in surface characteristics between wire cutting and machine-based processing also significantly influenced test results.
A breakthrough came out of thin air. A dedicated cutter for the curved spline was designed, enabling the gears to be processed accurately.
Manabu Ando (currently Senior Engineer, PTC Group Gearmotor Business Division Sales & Marketing Headquaters Product Development Department Product Development Section) talked about the team's struggles during this tough period. "We have the CYCLO® Drive, which is very durable and is the gold standard of durability when producing new Gear reducers with new mechanisms. We couldn't even make a cutter for the Gear reducer unless the design could be verified by testing.
The verification process of each gear prototype took a long time. It took several months to design the gears, design a cutter to make the gears, produce a prototype of the cutter and make the gears, and several more months to evaluate the durability of the prototype gears.
Despite these obstacles, producing prototypes with the cutters enabled the team to produce large quantities of gears with consistent accuracy, conduct more tests and gradually increase the speed of the development process.
Establishing a mass production system together
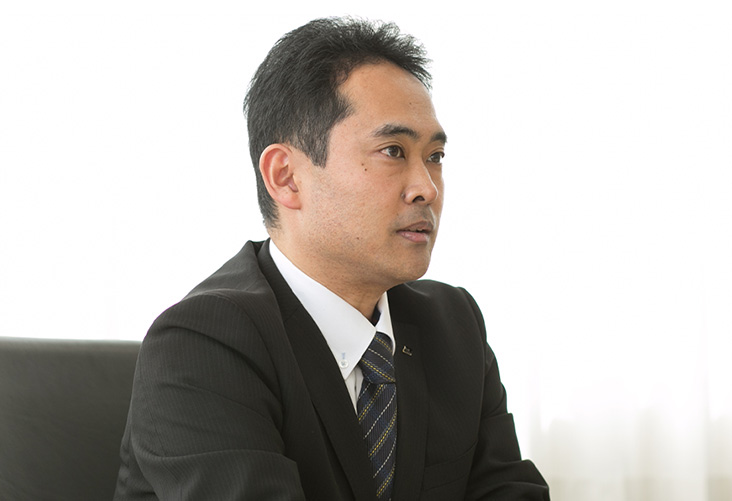
Even after gears could be produced with consistent accuracy, there were tremendous problems to overcome. If problems did not occur in durability tests of the curved spline, other problems occurred when the Gear reducer was assembled with other parts.
A breakthrough for these problems came in the form of a CAE simulation tool that had seen remarkable development in recent years. This tool was used to validate the design on a computer before the actual test. We also used a simulation tool developed by TRC to analyze the design under conditions that had not been considered in the past, which enabled a detailed evaluation of stress to which the Gear reducer was subjected. This significantly helped the progress of the development.
The simulation tool we developed is now being used to improve performance further.
The use of TRC's base of technologies saw the team gradually achieve the results they were seeking and finally complete the design for the ECY Series after struggling since the late 2000s.
However, the development was not completed yet. The team now had to establish a mass production system. Manabu Ando, who had been conducting research at the TRC, was transferred to the PTC Group to prepare this system.
Establishing a mass production system for the ECY Series was the top priority. Our senior management ordered the division to prioritize this first and foremost, and an organizational framework was established to facilitate cooperation between departments.
Suitable facilities and personnel training were essential to establish our mass production system. The first hurdle was that the existing facilities could not produce the new gears with the required accuracy, requiring the processing facilities to be improved. The new mechanism also required a new parts management system and assembly line. The whole division worked together and succeeded in establishing the system.
Nine ECY Series products are available as of December 18, 2019. The products are small in size, have a high rigidity, are highly safe and can be installed more easily in robots because the high-speed hollow shaft is larger, making it easier for electric cables to pass through.
A prototype has already been delivered to customers who are considering using this product, and has already received positive feedback.
The ECY Series is the result of more than 10 years of continued effort, the knowledge of the TRC and the cooperative organization framework that was put in place.
From industries to communities
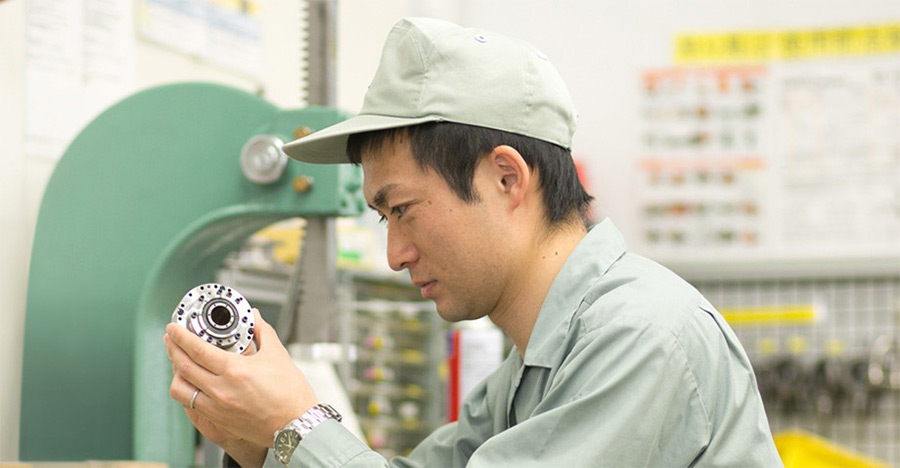
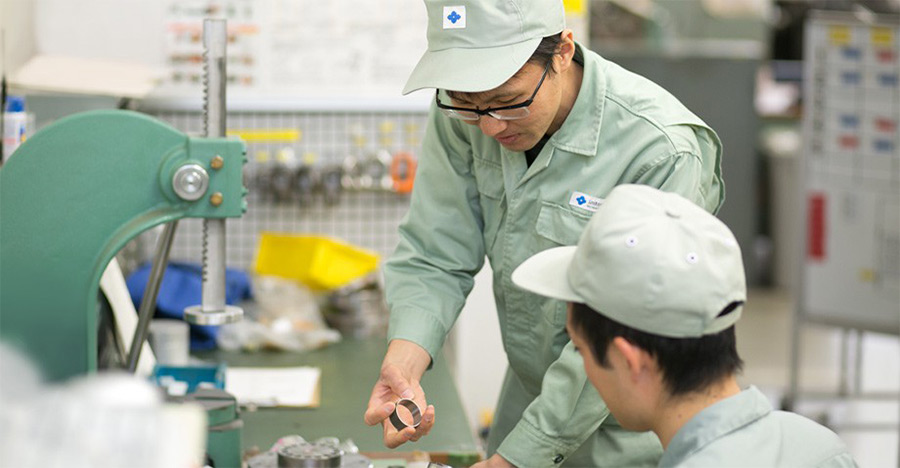
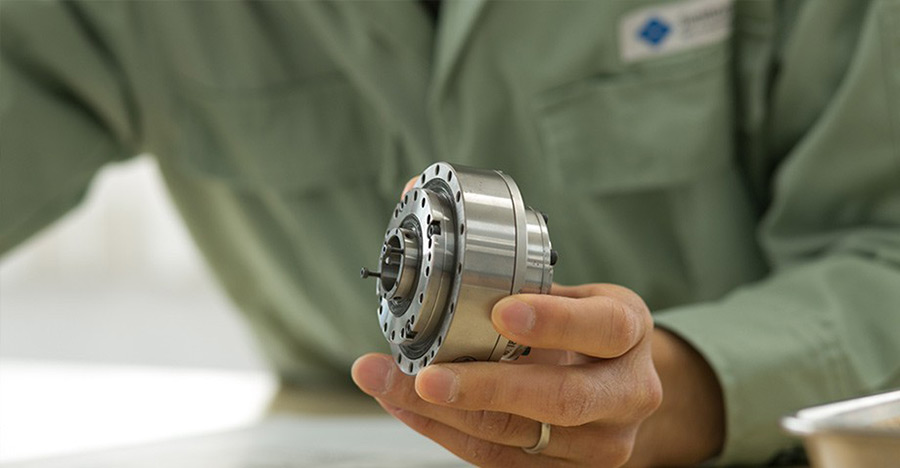
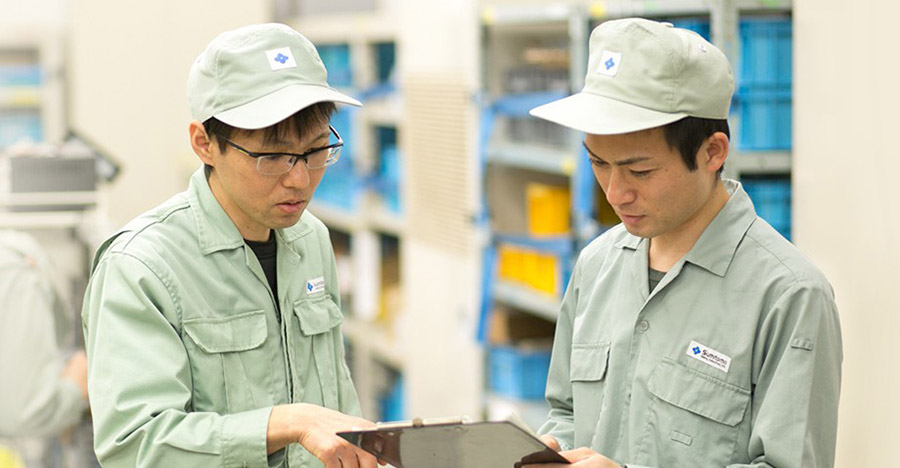
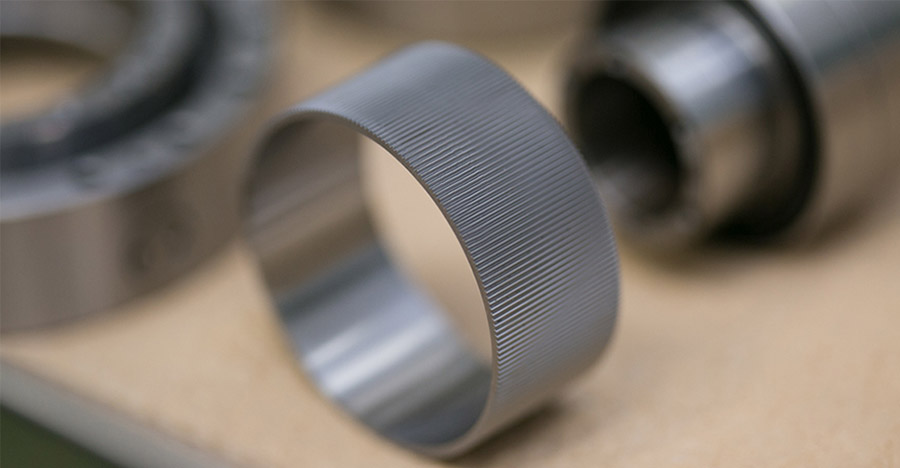
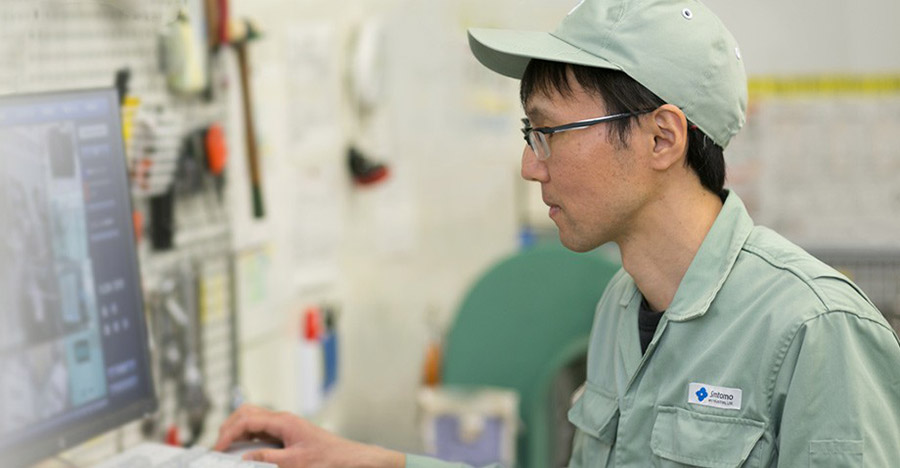
ECY Series Gear reducers are small in size and can achieve a torque output 1.5 times higher than that of conventional Gear reducers of the same size. While the team has yet to achieve its final goal, this product is already making a significant impact. In addition to working toward the final goal of double the performance, we are looking ahead to the near future-five or ten years from now-and developing smaller and better performing Gear reducers.
Thus far, the ECY Series has mainly been sold for industrial use, but the scope of application is set to grow in the near future. With birthrates declining and populations aging in countries like Japan, there will be a need for more robots working with members of the public, such as caregiving robots, medical care robots, power assist suits and AGV (automated guided vehicles). The requirements for these applications differ slightly from those of industrial applications: these Gear reducers must be ultra-lightweight and ultra-flat, with ultra-high accuracy and greater efficiency. We will need to continue building on our base of technologies to respond flexibly to these new needs among customers.
All three members of the team said that the development process of the ECY Series has been very valuable not only for gaining knowledge of product development for Gear reducers but also for understanding focal points in each element of technology development, including design, processing, and assembly.
During the long development period of more than 10 years, people were a driving force. Research and development never stopped, many employees continuously provided encouragement and the PTC Group as a whole worked together to achieve this goal.
In particular, the consultant who guided and advised the team from the beginning of the development process is a coach-like figure and the person to whom the team most wants to report the completion of development for the ECY Series.
The consultant came to TRC from Osaka twice a week since the development began. We thank him very much for his strong guidance from those amateur days when one could say that we were students. When we reported the wonderful news to him after the long development period, his response was one of encouragement: "I have been involved in various products but the release of the ECY Series has been my most rewarding moment! Thank you very much!
Now it's a matter of expanding the business. Keep developing this range-improve the performance and make derivative products-and make the ECY Series a new core business".
There were a lot of things we only just learned now, such as the fact that even the consultant was close to giving up on commercializing the series.
"He also told us 'The most important thing is to enjoy your work'. He told us to approach even routine work with a positive mindset, and that in order to get your colleagues on board, it's important to share everything you know. And this is exactly what the consultant continued to do for us for many years.
Finally, he said with a smile, "when the ECY Series becomes a core business, we'll meet again and look back on this happy moment."
With the technological base and strong team we have built during the long history of TRC and a good working relationship, we will be able to complete the ECY Series.
There is no doubt in our minds that TRC will develop more products to provide support for society.
*All contents are as of the time of the interview.
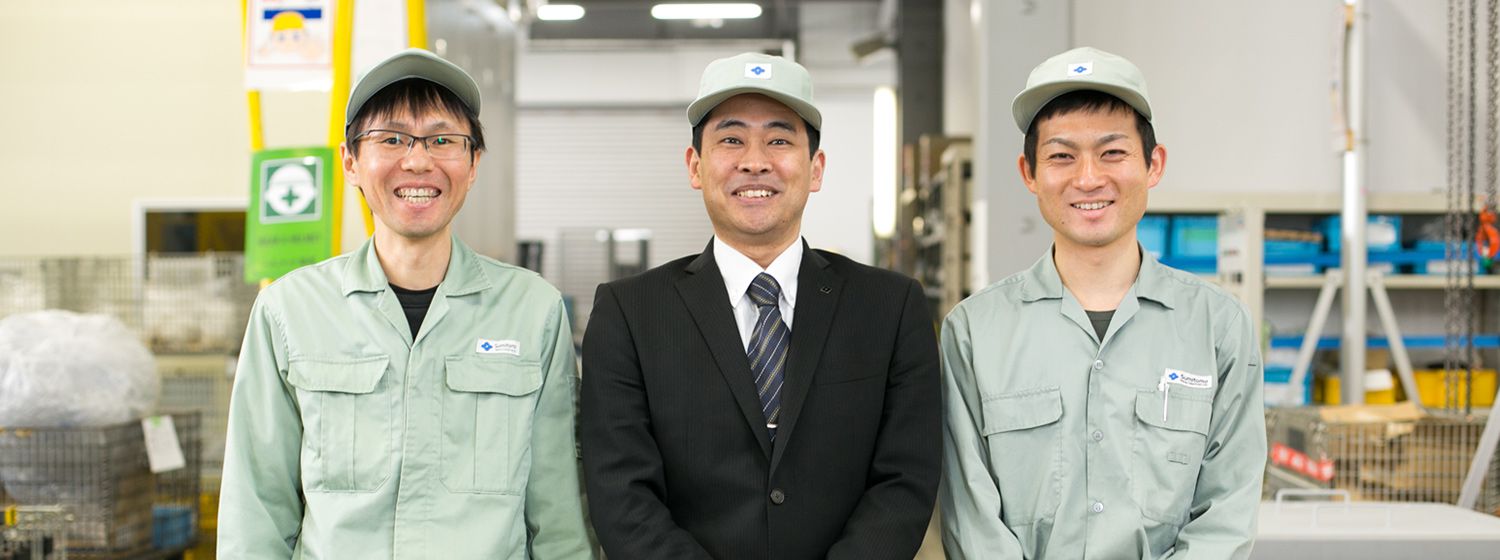
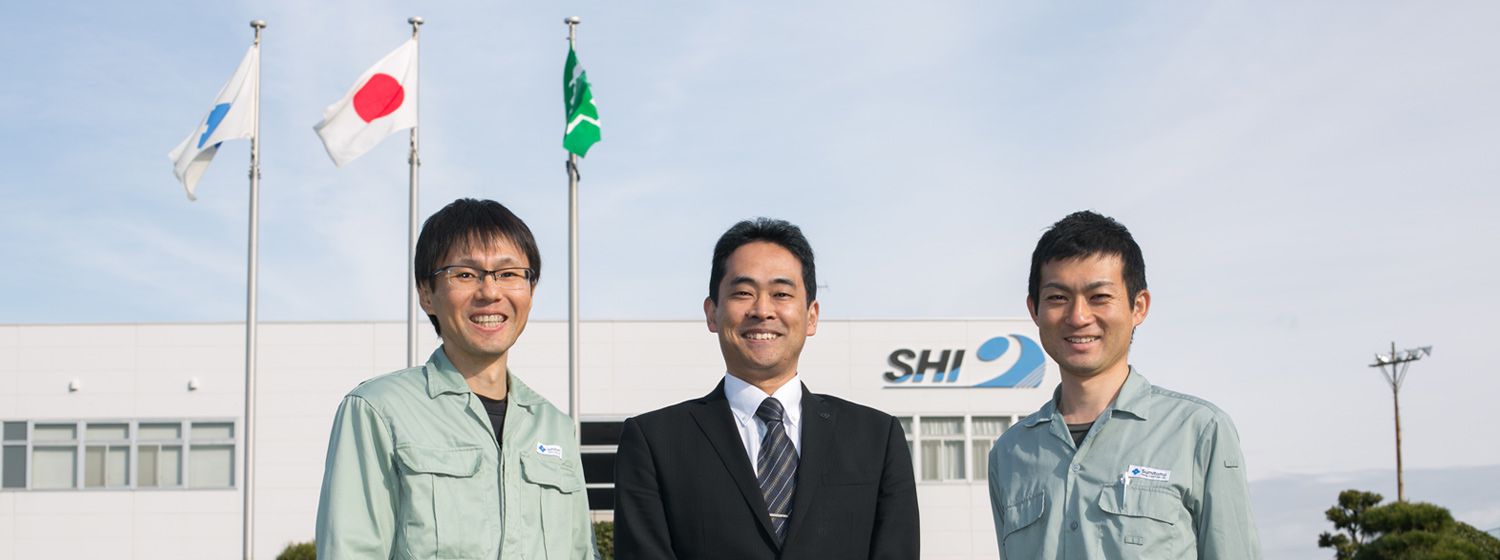
SHI Pride
- Vol.1 A Clear View of the Distant Heavens
- Vol.2 Cures without Surgery: Advanced Cancer Treatment
- Vol.3 Exploring the Mysteries of Space
- Vol.4 Dramatically Changing Quayside Cargo Handling
- Vol.5 Cyclo® Drives Continue to Evolve
- Vol.6 The Steam Turbine - Protecting the Environment and Advancing Society
- Vol.7 Persistent Determination to Reduce Defects, Losses and Faults to Zero
- Vol.8 Treating Cancer through the Use of Neutrons - A Compact Accelerator Opens the Door to Widespread Use -
- Vol.9 Automated storage system with unrestricted movement, for transforming the future of the logistics industry
- Vol.10 Anaerobic Wastewater Treatment and Biogas Power Generation System using Ume Seasoning Effluent bringing Recycling-Friendly Society