Persistent Determination to Reduce Defects, Losses and Faults to Zero
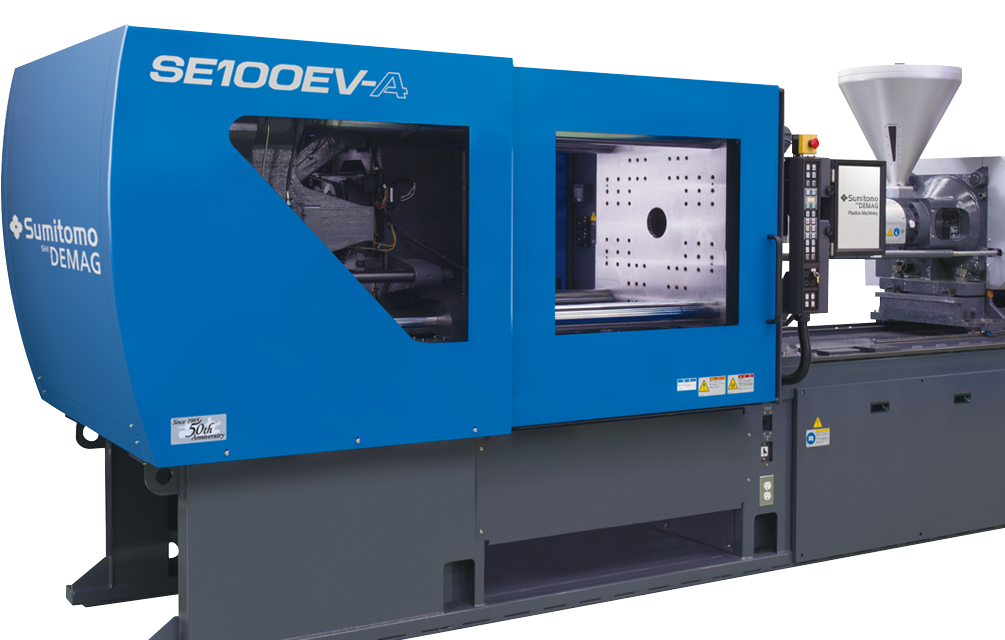
Injection molding is the conventional molding method for forming plastic products. The method involves resin melted and poured into a metal mold with pressure applied to fill the mold to form shapes. This is a suitable means for producing complex shaped products, ranging from plastic lenses for digital cameras to large components, such as automobile bumpers, in large quantities and at a lowS cost. Fully motorized injection molding machines from the SHI Group have attained top class achievements around the world. The "SE-EV" series, our latest series of products, received the Minister's Prize of the Ministry of Economy, Trade and Industry at the "33rd Excellence in Energy-Conserving Equipment Annual Awards" in 2012, as a result of positive evaluations for our activities into energy conservation over ten years.
Energy conservation, refinement and high productivity brought about by motorization
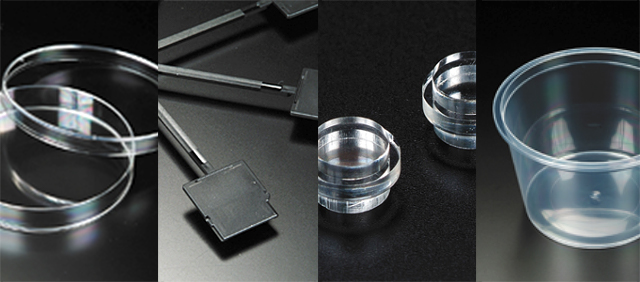
The history of injection molding machines at the SHI Group goes back more than 40 years. The very first unit was developed as specialized equipment for producing small plastic containers for lactic acid bacteria beverages in mass quantities.
Plastic containers made by injection molding can be produced in larger quantities and at a lower cost than glass bottle containers, while satisfying essential conditions for spreading beverage products all over Japan. This equipment is proudly exhibited at our manufacturing plant in Inage-ku of Chiba City, even to this day.
Previously the driving source of molding machines was fundamentally hydraulic pressure. However, motorization progressed during the 1990s with motorized products becoming the norm for manufacturers in Japan up until the present time. Since motorized equipment only needs to move mechanisms timed with the injection and mold clamping timing, they feature a better energy conserving performance in comparison with hydraulic equipment. One of the benefits is their ability to precisely position controls with servo motors.
The "SE-S" series of products launched in 1996 was the origin of the fully motorized equipment at the SHI Group. Great strides have been made since then to improve performance and the progress made is referred to as "Zero-Story". The "Zero" refers to "Zero Defects" in relation to burrs and other issues that could arise at any time at our production sites, as well as "Zero Losses" from the maintenance of molds and the like, in addition to "Zero Faults", in the setting up of arrangements to bring all these as close as possible to zero in order to increase productivity infinitely.
Innovation in molding process: "Zero-molding"
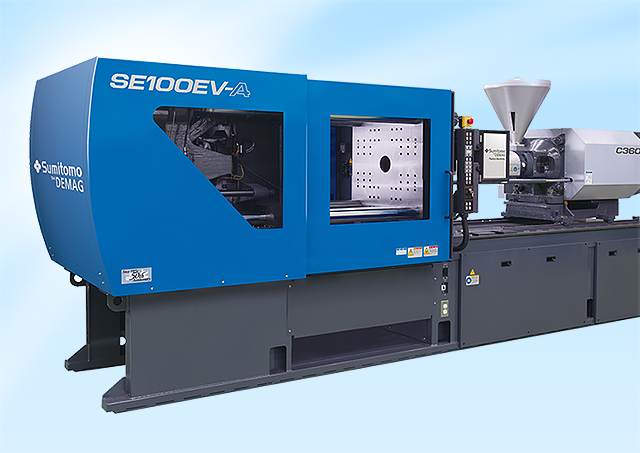
An innovative molding process, "Zero-molding", was incorporated for the "SE-DUZ" series of products, which were introduced in 2008. More precise control of the screw, which pushes out the material, was made possible by controlling the servo motor with a controller. Overfilling with too much material caused burrs, whereas too little resulted in an insufficient amount spreading throughout the mold. The "Flow Front Control" (FFC), one of the functions of the Zero-molding, optimizes the filling balance to deal with such concerns.
Furthermore, forming with a lower mold clamping force became possible through the detection of a minimally required mold clamping force, using the "Minimum Clamping Molding" (MCM) algorithm incorporated on the molding machines. This resulted not only in savings in the electric power consumption per work process but also enabled the implementation of machines with lower power output, leading to savings in expenses and electric power consumption for the manufacturing plant as a whole.
25% reduction in electric power consumption achieved through the evolution of machine structures
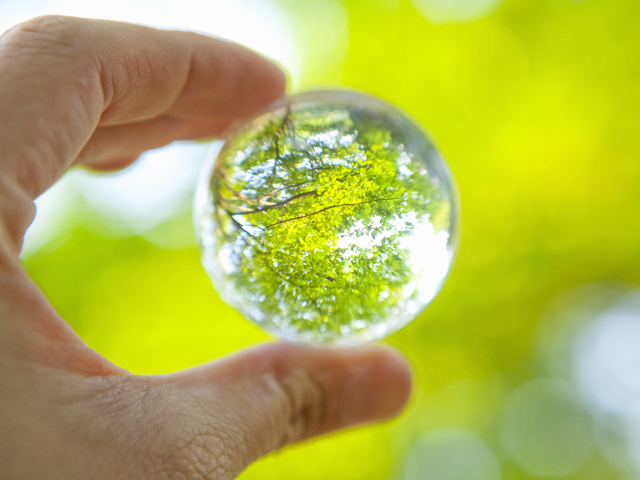
Such a concept of "Zero-molding" has evolved even further with the "SE-EV" series of products introduced in 2011.
The capability for sustaining the posture of the movable platen has been improved in order to enhance the effectiveness of the MCM function of the products of this series.
Previously a reaction force was generated in one direction when the nozzle of the injection machine was pressed against the movable platen creating a moment of force, which affected the posture of the fixed platen. The tilt was quite minimal but such a posture variation of the fixed platen became one of the contributing factors for wasted clamping force. The structure of the machines of the "SE-EV" series have been improved to receive such a reaction force against the nozzle in a symmetrical and uniform manner, which resulted in an inhibition of the change in posture of the fixed platen to its utmost limits. Therefore mold clamping could be performed with much less force.
Furthermore, posture fluctuations, due to clatter, have also been reduced by over 75% in the mechanical component for moving the movable platen, through the switching from "sliding guides" to "rolling guides". The recently implemented rolling guides have grease already sealed in so grease no longer scatters around the metal molds, which in turn significantly improves the environment for work and maintenance. The amount of grease discharged has been reduced to about half that of conventional machines.
Although these are just a small part of the technologies intended to conserve energy, new technologies, involving the changes of servo motors and the like, have been implemented to improve electric power consumption during operations and annual carbon dioxide emissions by 25% when compared with conventional machines.
More intuitive operations made possible with touch panels
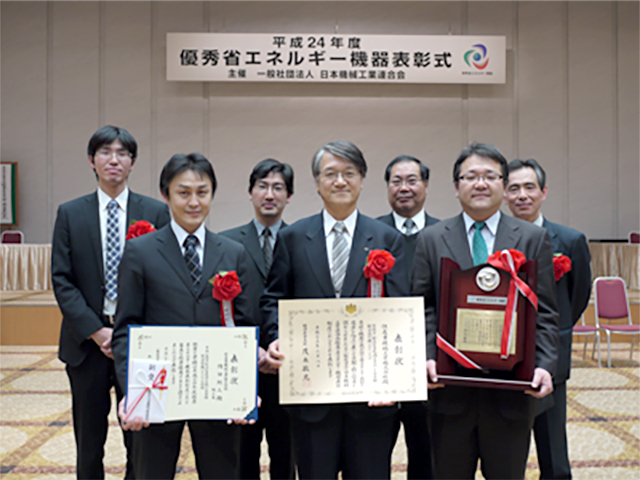
Methods have also been devised to improve operability for operators with the "SE-EV" series of products. Setting operations using the touch panel have been made more intuitive through the utilization of pictograms and a series of process operations can now be completed on one screen, which will likely reduce errors and the omission of settings. In addition to a minimization of the injection pressure and mold clamping force in the drive section, man-machine interfaces for such components have also been improved, which can be considered a significant advantage for these products.
The number of injection molding machines, supplied by the SHI Group, reached 40,000 units in cumulative shipments during 2004. Nearly 1,000 units of the latest "SE-EV" series of products, which are widely used in the automotive, precision machinery and medical fields, have already been sold (as of February 2013). The "SE-EV" series, our latest products, received the Minister's Prize of the Ministry of Economy, Trade and Industry at the "33rd Excellence in Energy-Conserving Equipment Annual Awards" in 2012, as a result of positive evaluations for our activities to conserve energy over ten years.
At the core of plastic forming manufacturing plants, injection molding machines work at a high speed of five to 20 seconds per cycle. We hope you are now aware of the fact that these machines are indeed a great collection of unexpectedly finely detailed precision technologies, even though at a glance they may appear unrefined.
- *All contents are as of the time of the interview.
SHI Pride
- Vol.1 A Clear View of the Distant Heavens
- Vol.2 Cures without Surgery: Advanced Cancer Treatment
- Vol.3 Exploring the Mysteries of Space
- Vol.4 Dramatically Changing Quayside Cargo Handling
- Vol.5 Cyclo® Drives Continue to Evolve
- Vol.6 The Steam Turbine - Protecting the Environment and Advancing Society
- Vol.7 Persistent Determination to Reduce Defects, Losses and Faults to Zero
- Vol.8 Treating Cancer through the Use of Neutrons - A Compact Accelerator Opens the Door to Widespread Use -
- Vol.9 Automated storage system with unrestricted movement, for transforming the future of the logistics industry
- Vol.10 Anaerobic Wastewater Treatment and Biogas Power Generation System using Ume Seasoning Effluent bringing Recycling-Friendly Society