Dramatically Changing
Quayside Cargo Handling
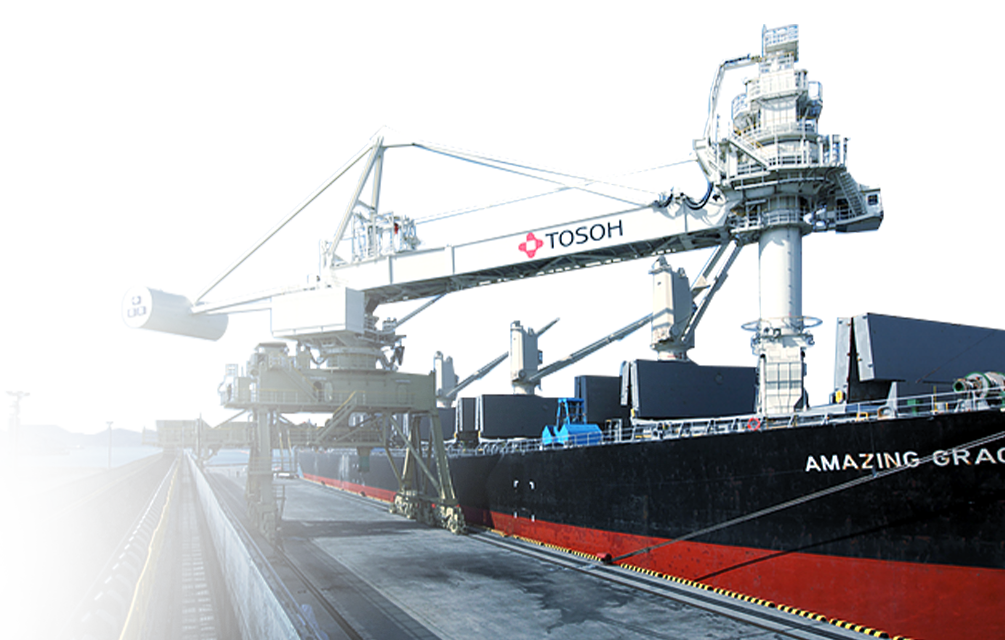
If you visit the wharves of a large port, you are sure to see enormous cranes busily loading and unloading cargo onto and off of ships. The cranes designed to unload loose bulk materials such as coal and iron ore from ships are called "unloaders." The SHI Group is a pioneer in the field of continuous unloaders and consistently maintains its position as a leader in the manufacture of this type of equipment.
Developers of Japan's First Continuous Unloaders-Meeting Demand for Greater Efficiencyand Reduced Environmental Impact
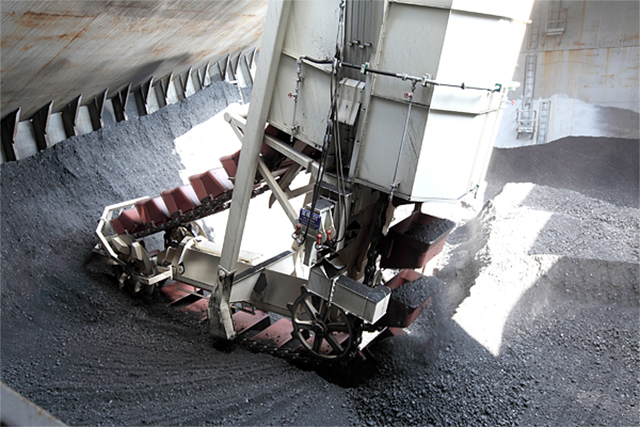
Unloaders, as the name implies, are a type of equipment designed to unload loose bulk materials from cargo vessels at ports. They are widely used to handle materials such as coal to be used as fuel by thermal power plants and iron ore to be used to make steel.
Previously, gantry cranes or so-called level-luffing cranes equipped with grab buckets were generally used to handle loose bulk materials. The bucket (a receptacle for grabbing and transporting iron ore, coal, etc.) was used to scoop up the bulk cargo and deposit it on the wharf, an operation that had to be repeated over and over.
As the volume of cargo being handled increased, however, the need arose for a way to unload large volumes of material in a short amount of time. Any increase in the unloading time has a direct impact on the shipping cost. There was also strong demand for environmental measures, for example to boost the energy efficiency of the cargo-handling equipment and to reduce the amount of dust scattered about by the process.
The "continuous" unloader was developed specifically to satisfy these requirements.
The first continuous unloaders to be domestically produced in Japan were developed and manufactured by Sumitomo Heavy Industries, Ltd. (now Sumitomo Heavy Industries Material Handling Systems Co., Ltd.) in 1976. The first generation had an unloading capacity of 300 tons per hour. By the 1980s capacity had increased to 1,000 tons per hour, and current models are able to unload iron ore at a rate of up to 3,500 tons per hour.
Support for Many Types of Bulk Materials as the Key Point
The structure of a continuous unloader comprises a lower base portion that travels on rails and a rotating portion on which is mounted a boom balanced by a counterweight. The rotating portion houses an elevator consisting of a continuous series of buckets attached to a chain. The bucket elevator scoops up bulk material while continuously turning.
The key point in technical development thus far has been adapting the unloading process to match the characteristics of the bulk materials being handled. For example, at a steel mill the bulk material being unloaded was iron ore, which had a higher specific gravity than coal, so the excavation resistance was greater. This meant that additional measures had to be taken to deal with wear. SHI engineers built a test system in-house, with a bucket elevator on the same scale as an actual unloader. Real iron ore was then unloaded repeatedly in order to determine the design conditions. This careful assessment of the risks associated with the unloading of iron ore can be said to be the main reason why SHI products deliver improved support for this type of bulk material.
Also, models released in recent years are shifting to electrical drive employing inverter control instead of hydraulic drive, which was the norm previously. This enhances both rotating and travel operation while providing a substantial reduction in maintenance costs.
Manufacturing ExcellAn Ongoing Pursuit of Maintenance-Free Convenience and Automated Operationence at SHI
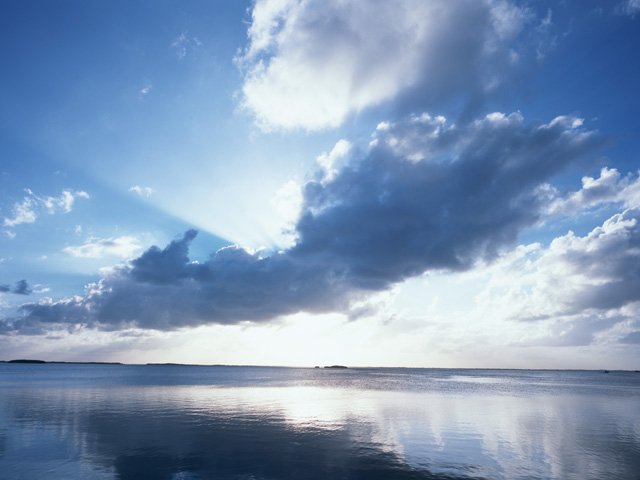
As a pioneer in the field of continuous unloaders, the SHI Group has been the leader in the domestic market. As Japan's port infrastructure ages, demand for replacement equipment is expected to be strong. The SHI Group also stands ready to meet the needs of facilities such as power plants and steel mills throughout the Asian region.
Some directions for new technology development include preventative safety systems for reducing maintenance costs and boosting the operating rate, and overloading prevention systems for protecting machinery. Development is also progressing in areas such as diagnostic systems that automatically estimate remaining service life by using sensors mounted on key components of the unloader.
The SHI Group also offers an optional teaching-playback system that makes possible more efficient unloading operation by initially remembering the necessary operations and then repeating them automatically. The SHI Group hopes to further extend globally the range of locales where its unloaders are active by adding more functional enhancements and technological innovations of this type.
- *All contents are as of the time of the interview.
SHI Pride
- Vol.1 A Clear View of the Distant Heavens
- Vol.2 Cures without Surgery: Advanced Cancer Treatment
- Vol.3 Exploring the Mysteries of Space
- Vol.4 Dramatically Changing Quayside Cargo Handling
- Vol.5 Cyclo® Drives Continue to Evolve
- Vol.6 The Steam Turbine - Protecting the Environment and Advancing Society
- Vol.7 Persistent Determination to Reduce Defects, Losses and Faults to Zero
- Vol.8 Treating Cancer through the Use of Neutrons - A Compact Accelerator Opens the Door to Widespread Use -
- Vol.9 Automated storage system with unrestricted movement, for transforming the future of the logistics industry
- Vol.10 Anaerobic Wastewater Treatment and Biogas Power Generation System using Ume Seasoning Effluent bringing Recycling-Friendly Society