The Steam Turbine - Protecting the Environment and Advancing Society
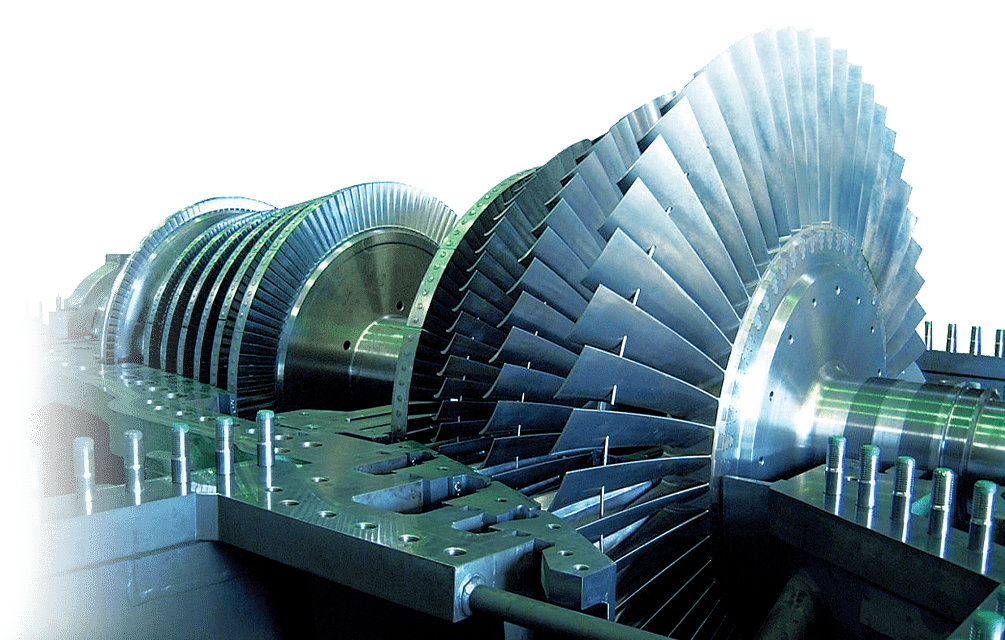
If you blow into a windmill, it turns very quickly. This is because the air from your lungs adds force into the rotor blades and makes the windmill rotate. Steam turbines also use the same principle to operate. This principle, which is said to pre-date Christ, is the foundation of steam turbines that have become a common, essential piece of equipment in many electricity generating facilities. Even then, technological innovation to make steam turbines more efficient, more reliable and lower in cost is continuing to take place.
The steam turbine born in
Kure City, Hiroshima Prefecture.
The essential driving force behind electricity generating facilities and factories
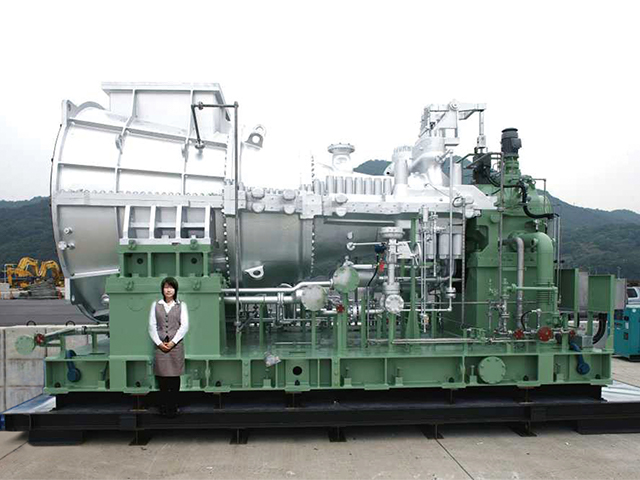
In a steam turbine, high pressure/high temperature steam that is generated from a boiler goes through a nozzle and is sprayed and expanded onto the surface of a rotor while the direction of the nozzle is set appropriately. The force of the steam creates rotational energy.
The rotation of the rotor can be used as power much in the same way as a waterwheel or windmill. Conversely, it can be used to turn a generator to create electricity. Today, the steam turbine has become an essential piece of equipment that drives fire-powered, nuclear, geothermal and biomass-fueled electricity generating facilities. In addition, the steam turbine is used as the propulsion device in many large-scale shipping vessels, and more compact models are being used to power the pumps and compressors in petrochemical plants.
In the SHI Group, the Kure City, Hiroshima Prefecture-based Shin Nippon Machinery Co., Ltd. is responsible for the development, manufacturing and sale of steam turbines. The products manufactured there are primarily used in captive power plants in general industrial facilities, with the most common fuel type being biomass.
Elemental technology research is done jointly by Shin Nippon Machinery Co., Ltd. and Sumitomo Heavy Industries, Ltd. There are many cases where Sumitomo Heavy Industries orders a full steam turbine module from Shin Nippon Machinery as part of the construction of a power generating facility.
By discharging steam in an axial direction, loss of energy is prevented.
A diverse product line-up that includes the "Axial Flow Emission Type" model.
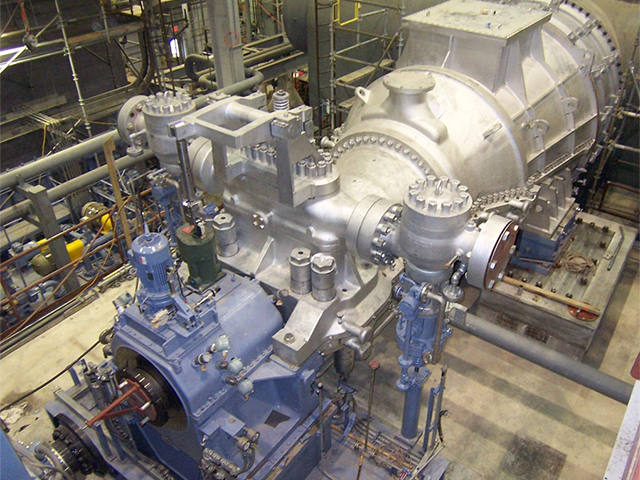
In steam turbines, there are several structural differences among available models.
After the steam is used up in a steam turbine, a condenser cold-condenses the steam to change it back to water so that it can be re-used again inside the boiler. A condensing steam turbine is one that makes the discharging pressure inside the turbine a vacuum during the condensation phase and captures and converts the heat from the steam into mechanical energy without waste. Compared to the non-condensing (or back pressure) steam turbines where the discharging pressure is greater than the atmospheric pressure, the condensing steam turbine is able to generate twice as much power.
The condensing steam turbines built by the SHI Group have an added structural improvement. In more traditional models, steam was discharged at a right angle to the rotor axis (either above or below) and returned to the condenser. However, discharge loss was found to be great when using this method, and moreover, if using a downward discharging system, the construction costs associated with the foundation and ventilation of a system that has to be equipped on high floors is prohibitive. If using an upward discharging system, low floor installation of the equipment is possible but the discharge loss was found to be greater, and the need for continued maintenance made it unfavorable.
With this in mind, we found that if steam can be discharged in an axial direction (i.e. horizontal) and the condenser can be directly linked to the system, the steam turbine can be installed in tighter spaces, and discharge losses can be minimized. From the maintenance standpoint too, this new design showed favorable results.
This design, known as the "Axial Flow Emission Type" steam turbine is packed with the technical and practical know-how of Shin Nippon Machinery Co., Ltd. The company boasts a product line-up of these Axial Flow Emission Type steam turbines that ranges from compact models that have a capacity of a few thousand kW to 100MW-class large scale models.
By having a product line-up that includes not only the Axial Flow Emission Type steam turbine but also the traditional downward discharging and upward discharging models, as well as the internal and external steam extraction models, we are able to meet the varying needs of our customer base.
Strong level of installation experience in biomass-fueled electricity generating facilities in Southeast Asia.
Playing a part in preventing global warming.
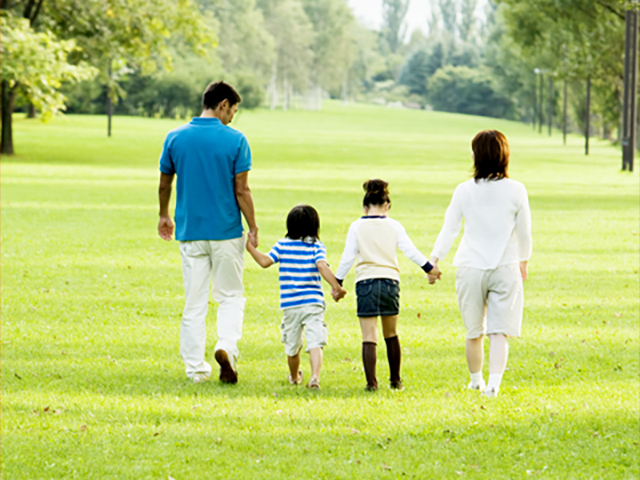
The structure of a steam turbine is quite large with the rotor, bearing, nozzle, and case forming the main components. Since high temperature steam that exceeds 550℃ passes through the equipment forming a severely difficult operating environment, meticulous attention to detail is required in all stages of the manufacturing and installation process including design, material procurement, production, assembly, testing, quality control, delivery, and installation. In particular, extra caution must be taken during the design and assembly of the few hundred turbine blades that are attached to the rotor to prevent injury or damage during the operation of the turbine. Some large-scale models even exceed three meters in external diameter which paints the appropriate picture with respect to the importance of attention to detail.
The SHI Group steam turbine that is most often installed in Japan is one that is combined with a waste incinerator. In this case, the heat that is generated from the burning of municipal waste inside an incinerator is then used to create steam, which in turn drives a steam turbine that generates electricity.
In more recent times, orders have come from overseas customers. In particular, Shin Nippon Machinery Co., Ltd.'s steam turbine technologies have been highly regarded by biomass-fueled electricity generating facilities in countries such as Thailand, Malaysia, Indonesia and other parts of Southeast Asia where electricity demand is high. As a result, the number of SHI Group steam turbines that are being installed in these countries is growing every year. At these facilities, the biomass being used is not just wood products but also agricultural waste products such as bagasse from sugar canes, which is grown readily in these areas, as well as rice husks. Moreover, we are seeing an increase in the prevalence of gas turbine combined-cycle electricity generating facilities that use natural gas as a fuel source and combine a gas turbine with a steam turbine to increase generating efficiency.
The principle behind steam turbines is said to pre-date Christ. Moreover, the technology to generate electricity from a steam turbine was introduced more than 120 years ago. Even then, technological innovation to make steam turbines more efficient, more reliable and lower in cost is continuing to take place as they have become an essential, high-efficiency piece of electricity generating equipment that is able to reduce the carbon dioxide emission footprint of entities and subsequently prevent global warming.
- *All contents are as of the time of the interview.
SHI Pride
- Vol.1 A Clear View of the Distant Heavens
- Vol.2 Cures without Surgery: Advanced Cancer Treatment
- Vol.3 Exploring the Mysteries of Space
- Vol.4 Dramatically Changing Quayside Cargo Handling
- Vol.5 Cyclo® Drives Continue to Evolve
- Vol.6 The Steam Turbine - Protecting the Environment and Advancing Society
- Vol.7 Persistent Determination to Reduce Defects, Losses and Faults to Zero
- Vol.8 Treating Cancer through the Use of Neutrons - A Compact Accelerator Opens the Door to Widespread Use -
- Vol.9 Automated storage system with unrestricted movement, for transforming the future of the logistics industry
- Vol.10 Anaerobic Wastewater Treatment and Biogas Power Generation System using Ume Seasoning Effluent bringing Recycling-Friendly Society